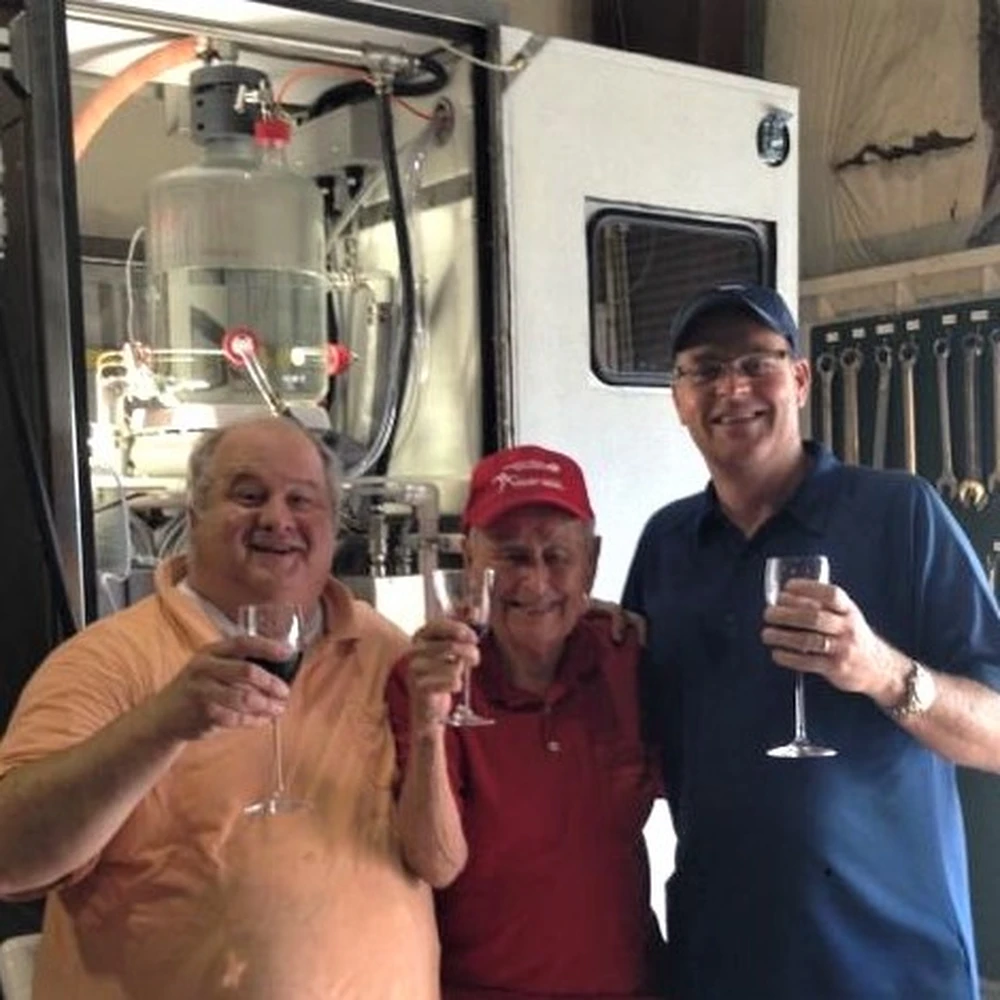
A patented technology that two Chemistry at Illinois alumni jointly developed to produce premium distilled spirits at much lower costs than standard methods has won a 2020 R&D 100 Award.
Greg George (BS, ‘82) and the late Benjamin Mosier (PhD, ’57, Laitinen) worked together for years on the innovative technology that has been recognized in the Process and Prototyping category by the R&D 100, an annual worldwide research and development competition that is widely recognized in industry, government and academia as a mark of excellence for the most innovative ideas of the year.
George is the senior research chemist and technology lead at Persedo, LLC, the small four-person company that’s now making this patented process commercially available.
Unfortunately, Mosier, director of research, passed away April 10, 2020, before their project was recognized with the R&D 100 award that was announced Oct. 1, 2020.
“I’ve never worked for anybody like him,” George said of his nearly 10-year working relationship with Mosier, who was in his 80s during the Persedo project. “He came into the lab every day feeling like he was going to win the Nobel Prize. He was very inspiring. He never gave up.”
A random phone call in 2010 brought the two alumni together.
A metallurgist in the gas and oil industry, George fielded a work call from Mosier, who was a consultant after a long, distinguished career as an analytic chemist at Exxon Research and an internationally recognized expert in multiple scientific fields, having developed new technologies that led to numerous patents, including equipment for NASA astronauts.
After making the Illinois chemistry connection, Mosier soon hired George to help develop the distilled spirits idea that Rick Ford, a Texas businessman with a history of entrepreneurial success in the oil industry, had asked Mosier to develop.
“It was this lucky, accidental U of I connection that really got me the job,” said George, who also credits his hire with the fact that he did undergraduate research for the late Illinois chemistry professor John C. Bailar Jr., whom Mosier also knew during his time at Illinois.
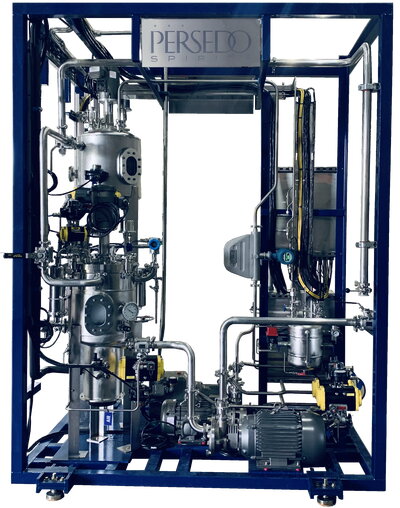
By modifying a simple vacuum pump, Ford’s late father had created a homemade device that essentially vacuumed out at atmospheric pressure volatile components in harsh scotch, improving the taste. Ford asked Mosier if he could try to develop his father’s idea.
“So, Mosier and I hurled ourselves into this,” George said.
Over the next five years of analysis and repeated trial and error in the lab, a key moment came when George recalled that as a chemist with the Illinois State Water Survey, he had used an ultrasonic transducer to remove gases from solvents for liquid chromatography. They incorporated a transducer into their design.
“The first time we ran it, there was a dramatic change in the overall taste of the spirit,” George said. “We could take Everclear, put it into our system and clean it up and make a respectable vodka out of it using the ultrasonic process,” George said.
The project also received support and scientific discussion from Illinois chemistry professor Ken Suslick, an expert in ultrasonic chemistry and one of the first to taste the Persedo product.
After more careful analysis and development, a second key moment came when they introduced carbon dioxide to the process.
“By switching gases, we were getting flavor esters out of the fatty acids. This is what a barrel does,” George said, referring to the long process of aging whiskey in a barrel. “We were doing the same thing in 20 minutes with the addition of carbon dioxide.”
In 2014, they finally had a refined process that very efficiently improved the taste of multiple types of alcohols, so they applied for a patent. Ford hired an engineer from the oil services industry to turn “this crazy lab process,” George said, into an actual functional system that could produce thousands of gallons of product a day. And with investors on board, they built a facility in Houston.
“We convert a neutral grain spirit, as it’s called, that’s essentially 98 percent alcohol and 196 proof into a product that can be made into a premium vodka in a single step. Normally, a distiller would have to take this product, distill it for 11-12 hours at considerable expense of labor and energy, lose 30-35 percent of the distillate in removing the undesirables and then take that heart cut and turn it into vodka,” he said. “We can save all of those losses in energy, labor and materials, by making an elite premium vodka in a single step.”
George said it was the first time in his career that he felt a real sense of adventure.
“I’m an average chemist, but I’m a persistent chemist,” he said, crediting Mosier as the force to fruition. “He was a task master. He came in every day expecting to accomplish something.”
George said his advice to Illinois chemistry students is that you don’t have to be a superstar, because it’s not what makes a satisfying life in research and development.
“My love of chemistry and my sense of adventure and excitement about it is what kept me going in the face of a whole lot of Bs and Cs, and I hope that chemistry majors will realize that sometimes it’s worth the struggle in a great program to just succeed and do the best you can and make a life for yourself that way,” George said, adding that he credits his passion for research and his Illinois chemistry training and connections with this remarkable success.